bretwashere
Member
- Joined
- Feb 2, 2023
- Messages
- 13
Hello,
I have a Macintosh IIsi, which up until recently was working completely fine. It does not power on, and I don’t hear any signs of life coming from the power supply. The computer has already undergone maintenance on the motherboard as far as a full recap on the motherboard, and I personally just recapped the power supply.
So after quadruple checking my work, the power supply recap definitely seems like a success. I do have a few questions for further troubleshooting:
1) There is a relay inside of the Sony APS-06 power supply. Upon switching the computer on with the power button, should this relay engage? I do not hear or see any activity with this relay upon pushing power. I’ll include an image at the bottom of this post to show the relay I’m speaking about.
2) Is there a way to check system power and power rails using the SCSI port (The DB-25 or the internal 50 pen cable)? If so, can anyone please provide me with steps to perform this?
3) I’m sort of new to the electrical engineering aspect of my life. With that being said, what would be everyone’s next step for troubleshooting? I have replaced the 3.6 V battery, I have completely disassembled and reassembled the system (cleaning everything in the process), try different power cables, reset the RAM, removed the PDS to NuBus adapter. I do own oscilloscope, but I haven’t have any experience with it. Does anyone have a guide for how to test the power supplies rails directly, or information regarding how to use oscilloscope to troubleshoot a 68K Mac?
Any help to further troubleshoot this issue would be appreciated.
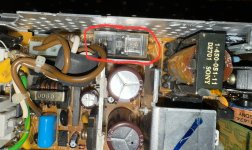
I also wanted to add that I did test continuity of the pins connected to the power button. They work as expected.
I have a Macintosh IIsi, which up until recently was working completely fine. It does not power on, and I don’t hear any signs of life coming from the power supply. The computer has already undergone maintenance on the motherboard as far as a full recap on the motherboard, and I personally just recapped the power supply.
So after quadruple checking my work, the power supply recap definitely seems like a success. I do have a few questions for further troubleshooting:
1) There is a relay inside of the Sony APS-06 power supply. Upon switching the computer on with the power button, should this relay engage? I do not hear or see any activity with this relay upon pushing power. I’ll include an image at the bottom of this post to show the relay I’m speaking about.
2) Is there a way to check system power and power rails using the SCSI port (The DB-25 or the internal 50 pen cable)? If so, can anyone please provide me with steps to perform this?
3) I’m sort of new to the electrical engineering aspect of my life. With that being said, what would be everyone’s next step for troubleshooting? I have replaced the 3.6 V battery, I have completely disassembled and reassembled the system (cleaning everything in the process), try different power cables, reset the RAM, removed the PDS to NuBus adapter. I do own oscilloscope, but I haven’t have any experience with it. Does anyone have a guide for how to test the power supplies rails directly, or information regarding how to use oscilloscope to troubleshoot a 68K Mac?
Any help to further troubleshoot this issue would be appreciated.
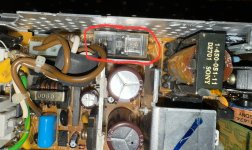
I also wanted to add that I did test continuity of the pins connected to the power button. They work as expected.
Last edited: